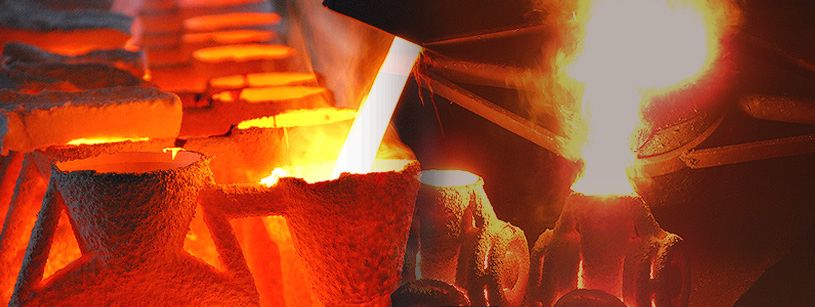
Indsur Global- Foundry Industry, puts Rs. 150-cr Plan on Hold
October 17, 2016
Why Castings? Introduction to Casting Procedure
November 7, 2016Casting is the process from which solid metal castings are produced by filling voids in molds with liquid metal. The basic steps involved in making castings are patternmaking, molding, melting and pouring, shakeout and cleaning, heat treating, and inspection.
Patternmaking
In casting terms, a “pattern” is a model of the object to be cast which is used to shape the mold cavity. They can be developed from a wide range of materials, like wood, plastics, or metal. Patternmaking is the process for creating these patterns. As the pattern determines casting form, a casting can be no better than the pattern from which it is made. To produce a quality casting, it is important that the pattern is carefully designed, finished, and constructed.
The main functions of a pattern:
- shape the mold cavity
- provide a means of delivering liquid metal into the mold (the gating system)
- provide accurate dimensions
- accommodate the characteristics of the metal cast
Molding
Molding is the process of making a mold to obtain molten metal. There are two types of mold processes: Reusable and non-reusable.
As the name suggests, reusable molds can be used repetitively. The casting process does not break down the mold at the time of metal solidification and cooling process. Reusable molds are generally made from metal.
Non-reusable molds are temporary objects that are destroyed. The most widely used non-reusable mold method is sand casting, a process in which specially treated sand is rammed around the pattern and placed in a support (flask). The pattern is then removed, cores are set in place, and the gating system is recognized to guide molten metal into the mold.
Melting & Pouring
There are main two categories of metals that castings are produced from: non-ferrous and ferrous metal. The metals to be cast and melted, usually a combination of recycled scrap and alloying metals – are loaded to “charge” the furnace. The metal is at extremely high temperatures until the melting point. Specialized furnaces are essential to reach elevated temperatures.
Two dominant kinds of melting furnace employed by foundries are electric arc and induction.
The electric arc furnace works as a batch melting process. Here produced batches of molten metal known as “heats”.
Induction furnace passes electrical energy – a high voltage electrical source from a primary coil induces high current in the steel charge, low voltage, or secondary coil.
Solidification, Ejection, and Cleaning
Pouring machines are used to move molten metal from one location to another. Expert metal workers will also pour molten metal using ladles. This metal is poured into the mold through a system; the metal cools and solidifies. The casting is then ejected from the mold, or removed from a sand mold.
The gates and risers that deliver metal to the mold interior also fill with molten metal in the process. The Metal in the mold solidifies along with metal in the gate and riser system, forming a single piece. Directly after ejection, metal from the gate and rider system is still attached to the main casting body. A mix of tumbling barrels, pressure washers, and air-blast units are used to clean off.
The resulting casting should be identical in shape and proportion to the original pattern, while it may be slightly smaller due to metal shrinkage.
Heat treatment and Inspection
Heat treating involves the use of heating and chilling, often to reduce stress in a cast part, to extreme temperatures, and/or modify the physical properties of the metal. The temperature must be controlled with precision to achieve the desired physical properties.
Castings can be considered complete before a production run, and its physical properties and structural integrity are checked. The testing methods used depend on how demanding the specifications are. Where for some purely aesthetic products, only a brief visual inspection for dimensional accuracy, cracks, and surface finish is required. If the casting will be required to perform in an industrial capacity, it may have all of its physical properties tested exhaustively.
Service Life and Recycling
After passing inspection, it is shipped, sold, and put into service. Produced cast metal products, especially those that have undergone heat treatment, are durable. Based on the metal alloy and application, its service life might range from a few months to several decades. When the service life of a casting ends, the cycle begins again.